AMERICAN COUNCIL OF ENGINEERING COMPANIES (ACEC)
Member firms are providing creative solutions to a variety of waterfront challenges
Reclaiming the Riverfront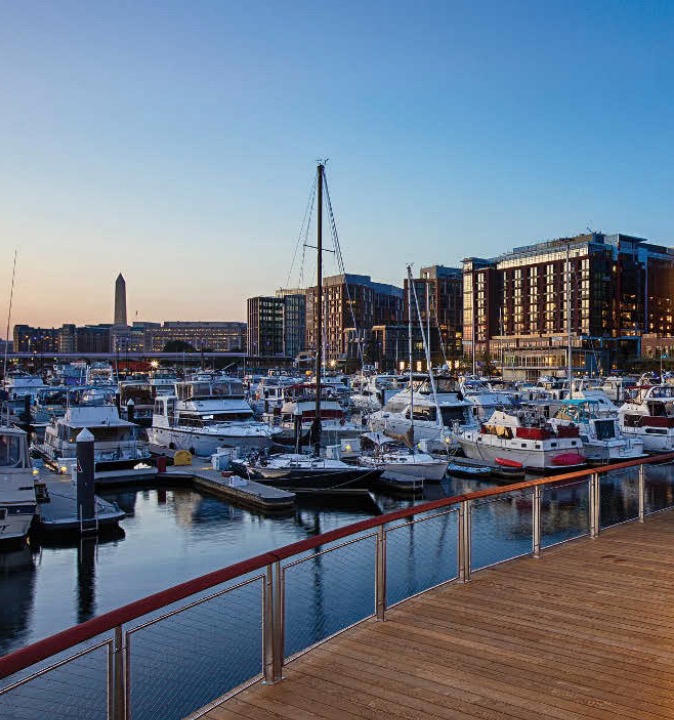
Project: The Wharf, Washington, DC
Firm: Moffatt & Nichol, Long Beach, CA
The District of Columbia took a bold step forward in reinvigorating the Washington Channel’s Southwest Waterfront as a vibrant community and destination waterfront. Known as The Wharf, the $2 billion redevelopment project incorporates the best of modern mixed-use urban design— waterfront public space, promenades, piers, docks and marinas, as well as ground-floor retail below a combination of condominiums, office space and entertainment venues.
Located in a dense urban setting with existing tenants, multiple stakeholders and overlapping jurisdictions, the project required a vast amount of planning, coordination and engineering. It also required an extensive entitlement effort, necessitating an act of Congress to decommission the federally owned channel—part of the Potomac River—so it could revert to city ownership and allow for the expansion of the waterside into the former channel.
Moffatt & Nichol was a key member of the development team, providing planning, permitting, market analysis, pro forma, grant application processing, structural inspections above and below water, design services and construction support for all waterside elements of The Wharf. These comprise project components from the sea wall waterward including repair of the existing sea wall, construction of four new public piers, three private piers, three recreational marinas, tall ship and water taxi facilities, and repair and expansion of the existing dinner cruise pier.
Although there is nothing simple about a project of this size and scope, especially in such a high-profile location, the owner and developer took a forward-looking approach to the opportunity.
“The Wharf was planned and designed not as an upland development that happened to have a waterfront component, but rather as a waterfront project where everything in the whole project is focused on that space where the land meets the water,” says Robert V. Sloop, senior coastal and waterfront project manager and engineer with Moffatt & Nichol. “That is a very unique approach. The design challenge then became determining how to maximize that interaction and how to provide a wide variety of experiences at The Wharf.”
The goal of developing waterside features to enhance the patron experience, draw people to the area and increase area property values did not simplify the engineering challenges of creating a viable waterfront destination with multiple activities—water taxis, tall ships, transient vessels, dinner cruises, human-powered watercraft and marinas—in an area with a limited maritime tradition.
Despite the challenges, Phase 1 opened in October 2016, three years after groundbreaking, and has become one of the area’s most popular destinations for both residents and tourists. Phase 2 is expected to open in 2022.
Balancing Protection and Environment
Project: High Island Waterfront Restoration, New York, NY
Firm: Langan, New York, NY
High Island, a small private island off the northeast tip of City Island at the eastern end of Long Island Sound, is home to radio transmission facilities broadcasting two of the largest AM radio station signals in the tri-state area. A multiyear waterfront restoration effort balancing hardscape protection with a soft edge has now established environmentally friendly shoreline protection for the island.
The waterfront restoration addressed issues along almost half of High Island’s shoreline including where previous stabilization efforts had not been successful.
Washout of slope was compromising the stability of the site’s perimeter security fence and the radio tower anchors. The erosion also was threatening the copper grounding system, a critical component of the transmission system.
Beyond that, the single-lane timber-framed bridge from City Island—the only access to the island—had undergone a significant upgrade in 2010, which included protecting the concrete eastern abutment on the island. However, erosion of the surrounding area continued, with washout behind the bridge headwall destabilizing the abutment and undermining nearby duct banks. This also was adversely affecting the asphalt service roadway, all of which put the ability to provide basic utility service and needed fuel transport to the island in jeopardy.
The complex wind, current and wave dynamics required a robust system to counter the environmental conditions, although the island location prevented the use of large-scale equipment and materials.
The desire to balance long-term protection with minimal maintenance requirements was only part of the challenge. The design and construction plan also had to satisfy environmental constraints to gain state and federal regulatory authorization, and there were practical timing and cost limitations.
The solution was a combination of traditional stone riprap and gabion baskets together with creating a living shoreline that uses green gabion baskets and plantings.
“We did the construction for the bridge abutment protection and utility protection, and some planting, in 2010,” says Gregory Biesiadecki, principal with Langan, which provided site assessment and developed the restoration plan. “But storms in 2011 wreaked havoc on a lot of the plantings. Our contractor replanted, but to provide more overall protection from the wave action, we also planted on the north side.”
Ultimately, gabion mattresses—wider and thinner than the standard gabion basket configuration—strategically located on the southerly end of the island provided the needed stability.
“These are more flexible, so if the soil does begin to erode, the mattress drapes down and continues to limit the potential for undermining,” says Biesiadecki.
The High Island waterfront restoration was completed in 2016. The living shoreline and plantings continue to be monitored for survivability and growth together with the performance of the shoreline protection.
Mixing Heritage and Elegance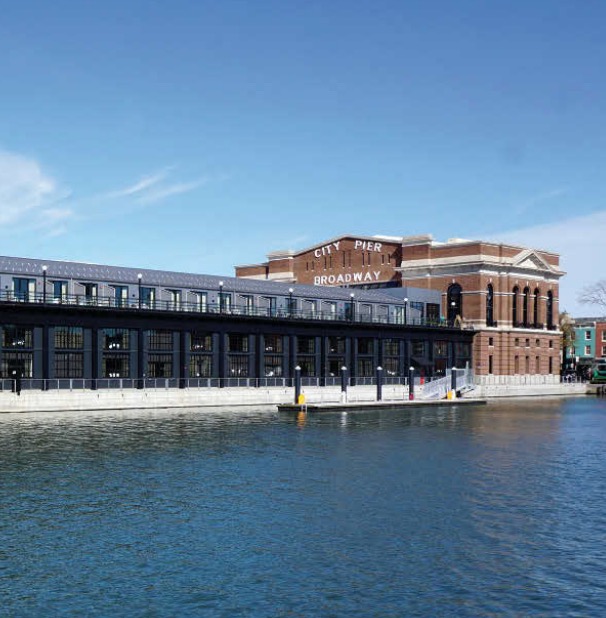
Project: Sagamore Pendry Baltimore Hotel, Baltimore, MD
Firm: Whitney Bailey Cox & Magnani, Baltimore, MD
Baltimore’s Recreation Pier opened in 1914 as a commercial pier. Located in Fell’s Point, across the river and just a mile upstream from historic Fort McHenry, Rec Pier was put to many uses over the years. Following World War II, it served as part of the country’s second largest point of entry after Ellis Island. By 2014, when Sagamore Development purchased the property, 15 years of continuous deterioration and disuse had turned the once-iconic headhouse and pier into a derelict structure.
Today it has been transformed into a three-level, 128-room luxury hotel that features world-class amenities while preserving a key part of the area’s history.
Whitney Bailey Cox & Magnani (WBCM) provided a complete structural, civil and marine engineering package for the renovation of the historic pier, and coordinated the design between the architect and the engineers.
The pier’s status as a registered historic building by numerous entities dictated many of the renovation parameters.
“We had to retain the steel substructure of the warehouse, as well as the entire headhouse, and renovate those,” says Mark Shafer, executive vice president with WBCM. “We could not just demolish the entire pier and build new, which probably would have been easier.”
WBCM’s innovative design reused the existing structurally deficient pier as formwork for a new pier. New piles were driven through holes cut in the existing pier, and a new 24-inch structural concrete deck was poured in two 12-inch lifts. The new structural two-way slab encapsulated all base plate connections of the existing historic columns and transferred the load to the new pile caps. The fast land bulkhead portion of the old pier was encapsulated with new steel sheet pile Baltimore’s renovated historic Recreation Pier is now home to the three-level, 128-room luxury Sagamore Pendry Baltimore Hotel. bulkhead and concrete cap beam with a soil anchor and transverse tie rod system. The combination of the bulkhead section and pier marine structural renovation accommodates the hotel, an interior courtyard, an extended deck and an integrated infinity pool.
The headhouse work included restoring, replacing or reconstructing all brick and stonework and all wooden windows and interior restoration. After determining the structural integrity of the existing structural steel framing, WBCM incorporated much of it into the hotel design. A new second hotel floor was placed between the existing first floor and the high bay roof, and the existing high bay roof framing was modified and reused to support the hotel’s third floor—both key elements in meeting the requirements of the Maryland Historic Trust.
Also, the at-grade level of the renovated structure was raised 3 feet to get above the 500-year Design Flood Elevation, and the exterior of the building was flood-proofed above the 500-year Flood Protection Elevation.
Preserving Coastal Heritage
Project: Wood Island Life Saving Station and Waterfront Restoration, Kittery Point, ME
Firm: Tighe & Bond, Portsmouth, NH
Situated on a small rocky island at the mouth of the Piscataqua River, between New Castle, New Hampshire, and Kittery, Maine, the Wood Island Life Saving Station for many years served as a base for those who went to the aid of mariners in distress in this busy shipping channel. Built in 1908, the station later was used to defend the harbor, then decommissioned after the end of World War II.
In 1973, the Town of Kittery took possession of the island from the federal government. The station had been unused and vacant since 1948 and continued to deteriorate until the Wood Island Life Saving Station Association (WILSSA) spearheaded a renovation effort.
The project includes restoration of the original station building, a dock and marine railway for lifeboats and replacement sea walls. WILSSA plans to establish a public maritime museum in the fully renovated station and build a replica lifeboat that can be launched from the station’s restored marine railway.
The most recent phase of the project, completed in the summer of 2018, was the restoration of the badly deteriorated sea wall along the island’s north side. Logistics were a major challenge. All equipment and materials had to be brought in by barge, timed to coincide with the tides, which made transporting concrete trucks very difficult. Because of that, the use of castin-place concrete was limited to rebuilding the sea wall foundation. Massive blocks of precast high-performance concrete were then placed and tied together using fiberglass rebar dowels secured with epoxy to form the sea wall.
“The sea levels traditionally have been rising about a foot every hundred years,” says Duncan Mellor, principal coastal engineer with Tighe & Bond. The firm did sea wall assessments for WILSSA in 2012 and subsequently provided full permitting and design for the entire Duncan Mellor Principal Coastal Engineer Tighe & Bond waterfront restoration. “Because we have already had a foot of sea level rise since the original sea wall was built, and the point of the project is to protect the island for the future, we made the new wall 2 feet higher than the old one.”
The Maine Army National Guard’s services were instrumental to the rapid construction of the north sea wall.
“The challenging location of the project—a small island off the coast of Maine—and the type of work involved were two of the things that appealed to the guard,” Mellor says.
Approximately 60 members of the guard’s 136th Engineer Company spent the month of June participating in an Innovative Readiness Training to provide cost-free construction labor for the sea wall project. The guardsmen set up a temporary camp at nearby Fort Foster and worked seven days a week, donating approximately $500,000 in equivalent wage labor. Besides rebuilding the sea wall and importing 600 tons of rock fill, they also rebuilt the historic shed and installed rough electrical and plumbing throughout the station.
Download full article (PDF): Waterfront Restoration and Redevelopment
Download full November/December issue of Engineering, Inc.
About the American Council of Engineering Companies
www.acec.org
The American Council of Engineering Companies (ACEC) is the voice of America’s engineering industry. Council members – numbering more than 5,000 firms representing more than 500,000 employees throughout the country – are engaged in a wide range of engineering works that propel the nation’s economy, and enhance and safeguard America’s quality of life. These works allow Americans to drink clean water, enjoy a healthy life, take advantage of new technologies, and travel safely and efficiently. The Council’s mission is to contribute to America’s prosperity and welfare by advancing the business interests of member firms.
Tags: ACEC, American Council of Engineering Companies, Engineering Inc., Redevelopment, Restoration, Urban Renewal, Waterfront